Miniature intricate for electromagnetic, e-drive, electric, pumps systems.
ASCO sintering services can be used to make a great number of mechanical and hydraulic structural components. Our parts have been used in complex electromagnetic applications like linear actuators, e-drive traction motors, electric motors, and electric pumps. Net shape tool designs provide 75% cost savings over traditional machining.
Powder Metallurgy – or PM is a state-of-the-art metal forming process for making net-shape components. After tool steel or carbide tooling is used to compact elemental or alloyed ferrous and non-ferrous powders, the resultant shapes are then sintered (heated) in a controlled reducing atmosphere furnace resulting in metallurgical particle diffusion bonding. A “chipless” metalworking process, PM typically uses more than 97% of the starting raw material in the finished part conserving both energy and material.
- Maximum Cost Savings
- Tight tolerance capability
- Six Sigma and lean manufacturing methodologies
- Collaborative creative tooling design
- High performance engineered materials
Case Studies
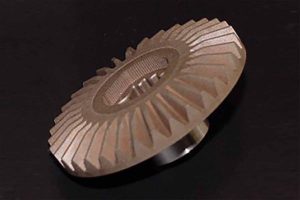
Bevel Gears
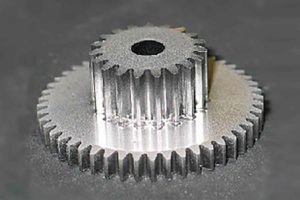
Double Gears

Gear Carriers with Integral Posts
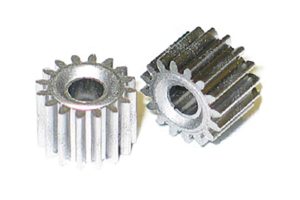
Spur Gears
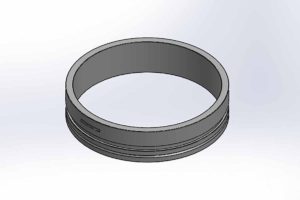
Bearing Sleeves
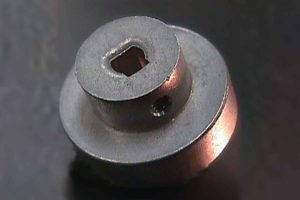
Drive Hub
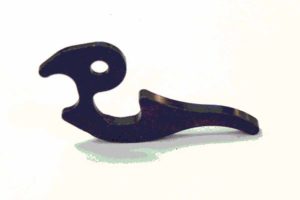
Ejector Handles

Pinion Gears
Automotive
ASCO supports the use of sintered metal in the advanced automotive market. Our customers are leaders in the automotive, hydraulic, pneumatic, and fluid power vehicle manufacturing industry, and they are utilizing our services to support the need for 3D printing, from functional prototyping to creating manufacturing aids to produce limited runs of production parts.
We have supplied the automotive industry with over 10 million powder metallurgy sintered metal parts. We use Six Sigma and lean manufacturing methodologies to create high-performance, high strength engineered materials. Shift-by-Wire, shock absorbers, brake systems, seating, and other complex automotive parts are manufactured by ASCO.
- Maximum Cost Savings versus MIM and CNC
- Tight tolerance capability required for automotive use.
- Six Sigma and lean manufacturing methodologies
- Collaborative creative tooling design
- High performance, high strength engineered materials
- Complex automotive components for Shift-by-Wire, airbag safety restraints, shock absorbers, brake systems, seating, exhaust systems, fuel monitoring and instrumentation systems
Case Studies
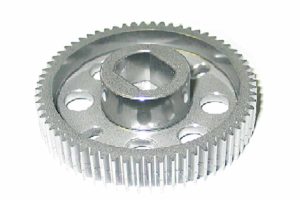
Shift By Wire – Sintered Components
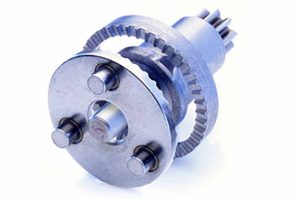
Minivan Door Clutch Assembly

Four Wheel Driving Shifting
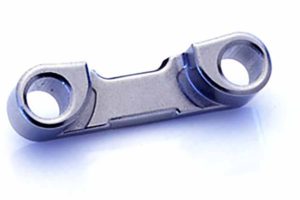