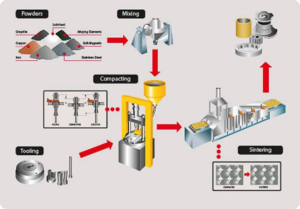
- Continuous Belt Furnaces
- High Temperature Pusher Furnace
- Temper & Annealing Furnaces
- Coining, Plating, Machining
A controlled amount of mixed powder is automatically gravity fed into a precision die mounted in a special mechanical or hydraulic press and compacted, usually at room temperature, to achieve the density requirement for the powder being pressed.
Compacting the loose powder produces a “green compact” which with conventional pressing techniques has the size and shape of the finished part when ejected from the die and sufficient strength for in process handling and transport to the sintering furnace.
Sintering
The typical sintering step, the green compact, placed on a mesh belt, moves slowly through a controlled atmosphere furnace. The parts are heated to a temperature below the melting point of the base metal, held at the sintering temperature, and then cooled. Basically a solid-state process, sintering transforms compacted mechanical bonds between the powder particles into metallurgical bonds. This provides the PM part’s primary functional properties. Typical sintering temperature ranges are 1,450°F-1,550°F for bronze and 2050°F-2100°F for ferrous alloys. Throughput varies with part size, belt width, and belt speed, reaching as high as 1,000 LBS/hour (450 Kg/hour) in large furnaces.